Although the range of valve products involved in the development and transportation of oil and natural gas has remained basically unchanged over the past century, valve manufacturers have been constantly updating their valve technology and actively responding to changes in the oil and natural gas industry market. To stay ahead in the market or not to be left behind, valve manufacturers are constantly updating the valve design, manufacturing, service, sales technology and process. The fact is that oil companies are demanding more and more from valve manufacturers: Valve Manufacturers must be good at solving the problems oil companies face on the basis of reasonable prices, and in the case of worse working conditions and more stringent environmental requirements, extend the performance of valve products to provide more service capacity. (1) the demand for oil and natural gas in the metal sealing market is increasing rapidly, and the footprint of developing crude oil has traversed every corner of the earth. For example, ultra-deep well technology poses challenges to equipment at ultra-low temperature and ultra-high pressure. The extraction of heavy crude oil is a profitable option, especially at $30 a barrel. High concentrations of ASPHALTENES and other impurities present difficulties in the transportation and processing of crude oil. In general, the soft-sealing ball valves used in oil pipelines can not meet the requirements of operating conditions. This requires valve manufacturers to develop metal-sealed ball valves and be able to adapt to changes in temperature and pressure, even in the transport of solid media (hydroxide, coke, etc.) to ensure that the absolute seal. And the metal seal technology benefits from the development of surface spraying technology. Valve manufacturers want to use this technology to maintain market leadership and spray technology as a development strategy, they and research institutes, universities, they hope to develop the next generation of "super hard" coating. (2) explosion pressure relief. In 2002, the API 6d standard of the American Petroleum Institute stipulated that Valve Products with design pressure higher than ASME Class 600 must be designed to be explosion pressure relief. Explosive Decompression refers to the phenomenon that when the pressure in the valve drops rapidly, the Co 2 which permeates the seal under high pressure expands rapidly due to the decrease of the pressure, resulting in seal explosion and rupture during the valve closing process, thus leading to valve failure. An oil company on a deep-sea platform found a valve explosion decompression phenomenon, valve failure after the company had to stop operation for several weeks to replace the valve, resulting in heavy losses. Since then, oil companies have required valve manufacturers to provide high-pressure valves with anti-"explosion decompression" configuration. In response, valve manufacturers quickly developed explosion-pressure relief seals and explosion-pressure relief valves to meet stringent environmental requirements. (3) the corrosion of Sour crude the high price of sour crude oil makes oil refining companies focus on sour crude oil, the investment and development of Sour crude oil market is profitable, in the long-term supply contract price competitive advantage. However, the presence of H 2s in Sour crude poses a new challenge to the corrosion resistance of the equipment. Valve manufacturers can provide ISO15156 approved materials, but also provide test (according to ISO15156) data to prove the valve material corrosion resistance and long life, the user put these valve manufacturers on the list of corrosion resistant valve suppliers. (4) ISO 15848 specifies the requirements for the design of fugitive emissions from valves, and manufacturers have redesigned the packing and sealing arrangements for general valves and special valves to meet newer standards. But the new standards are too general and stringent, so many oil companies have their own emissions standards, such as many North American companies that refer to API 622. The further improvement of valve fugitive emission standard needs the cooperation of valve manufacturer, user and standard-setter, which can learn from each other and solve the problem together. (5) early wear and equipment fatigue in pursuit of economic benefits, many oil refining enterprises are overloaded operation. The result has been endless additions to production equipment and modifications to systems. The enterprise's expectation of the equipment is far beyond the original design, which requires the valve manufacturer to take the initiative to participate in the user's work, avoid unreasonable design of the production process on the valve reliability, life and safety of the adverse effects. For example, valves used in thermal cycling systems tend to cause part thermal fatigue, and valve manufacturers with industrial process experience will arrange valves to minimize the possibility of problems. (6) preventive maintenance in order to ensure production, oil enterprises require the arrangement of equipment maintenance cycle. With the development of Valve test system, electronic hardware and software, valve preventive maintenance has been changed from an intelligent concept to a reality. A small number of valve manufacturers proficient in automation provide data analysis systems that quantify valve operation and provide valve preventive maintenance time. (7) the automation of oil refining process with automatic actuator is the trend of the times, and the control technology has been developed for a long time. The valve manufacturer installs an actuator on the valve to meet the automatic control production requirements. The technology of automatic actuator has been greatly developed. On the other hand, the manufacturer of the actuator also provides the valve product with the actuator to the user. As a result, the trend toward the integration of actuators and valves poses a challenge to a single manufacturer, after all, users want to find a company to solve the problem more easily, to avoid a split phenomenon. (8) Pipeline Ball Valve natural gas transportation pipeline engineering is a very large and potential market for valves. It is very important to monitor the long-distance pipeline. Some companies have developed smart devices that users can use to detect pipelines. Like "smart pig. ". The robot can detect wall thickness and even corrosion spots. However, the detection device for the pipeline size requirements, so the size of the ball valve has become the long-distance pipeline company's preferred products. On the other hand, the long-distance pipeline needs the valve wall thickness as thin as possible, the valve material has the very high yield toughness, the corrosion resistance, adapts the pipeline expansion, the turning, the local environment change request. It is important that long-distance pipeline managers require the purchase of valve life must be longer than the life of the pipeline itself.
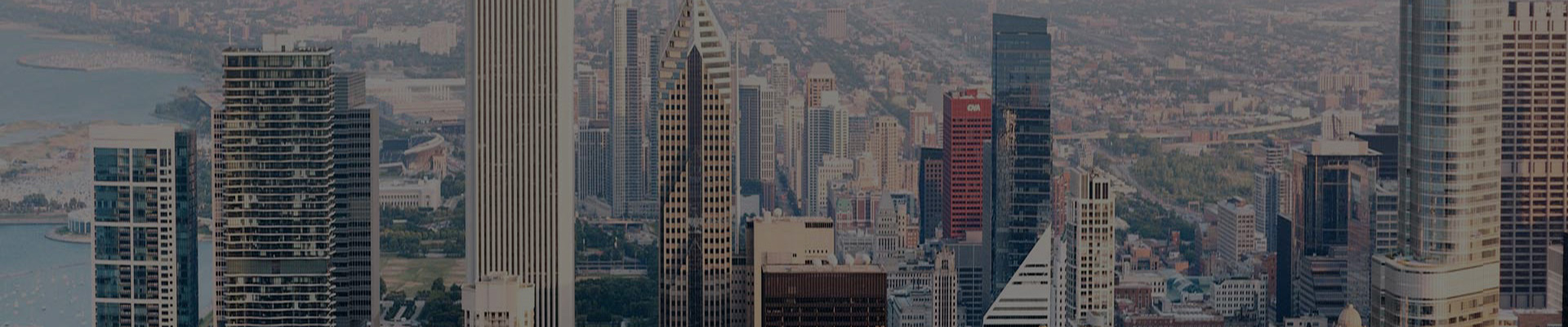
The change of oil and gas industry market the influence of the valve
Next :
None
Next :
None
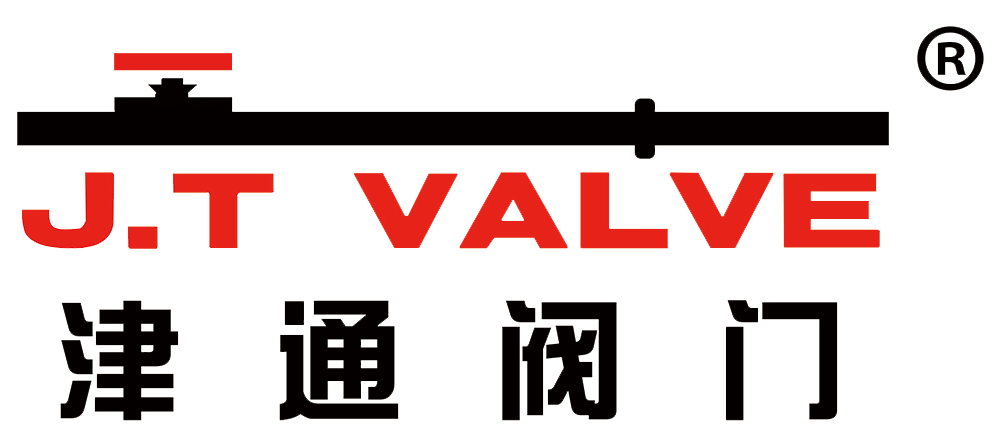
Factory direct sales/quality assurance/cash supply
Marketing network is the basis of enterprises occupy the market, win the competition
Product has a complete quality assurance, and outstanding cost performance
TEL:15822576587
E-Mail:47567183@qq.com
Address:Tianjin binhai new area of Marine high-tech development zone, 519 huashan road